Our Products and Services
Aerosphere specializes in surface treatment by compressive shot peening on metal parts, predominantly in the aerospace industry and industrial energy production sector.
Compression Peening (Shot Peening) involves projecting micro-beads of steels, glass or other various media on the surface of the metallic component surfaces to improve performance and technical qualities.
We offer in combination or separately:
Saturation Shot Peening
Saturation Shot Peening helps increase fatigue life of various structural components (wings, components with high levels of torsional or axial stress, etc.), landing gear, aircraft engine components, industrial gears for industrial power unit components, etc., giving them greater resistance to cracking and extending their useful life.
Useful on any metal component whose function is to undergo repetitive, constant stress, or which is close to the maximum tolerable limit for this type of material. Can also be used to improve the adhesion of subsequently applied paint-type primers.
Maximum capacity of 31' x 5.8' x 1' or 13.07m x 1.78m x 0.3m
Shot Peen Forming
Shot Peen Forming alters the profile of a component without modifying the mechanical properties, such as the wing skins, wing structure, or stabilizer. This is an ideal process for medium to large components with complex shapes, where 5-axis machining is not possible or is not cost efficient. Peen Forming can be applied with or without Shot Peening.
Maximum capacity of 31' x 5.8' x 1' or 13.07m x 1.78m x 0.3m
Shot Peen Straightening
Shot Peen Straightening makes it possible to straighten components (machined or otherwise) without changing the original mechanical properties of the manufactured base material. This technique is mainly used on monolithic machined parts when the result of the Shot Peen releases the induced residual stresses of the milled raw material or the machining. This method can also be utilized as a strategy for reducing costs at machining. In this case, Peen Straightening is used in conjuncture with various machining technique to improve machining time and increase the overall part quality by providing final configuration shape control.
Maximum capacity of 31' x 5.8' x 1' or 13.07m x 1.78m x 0.3m
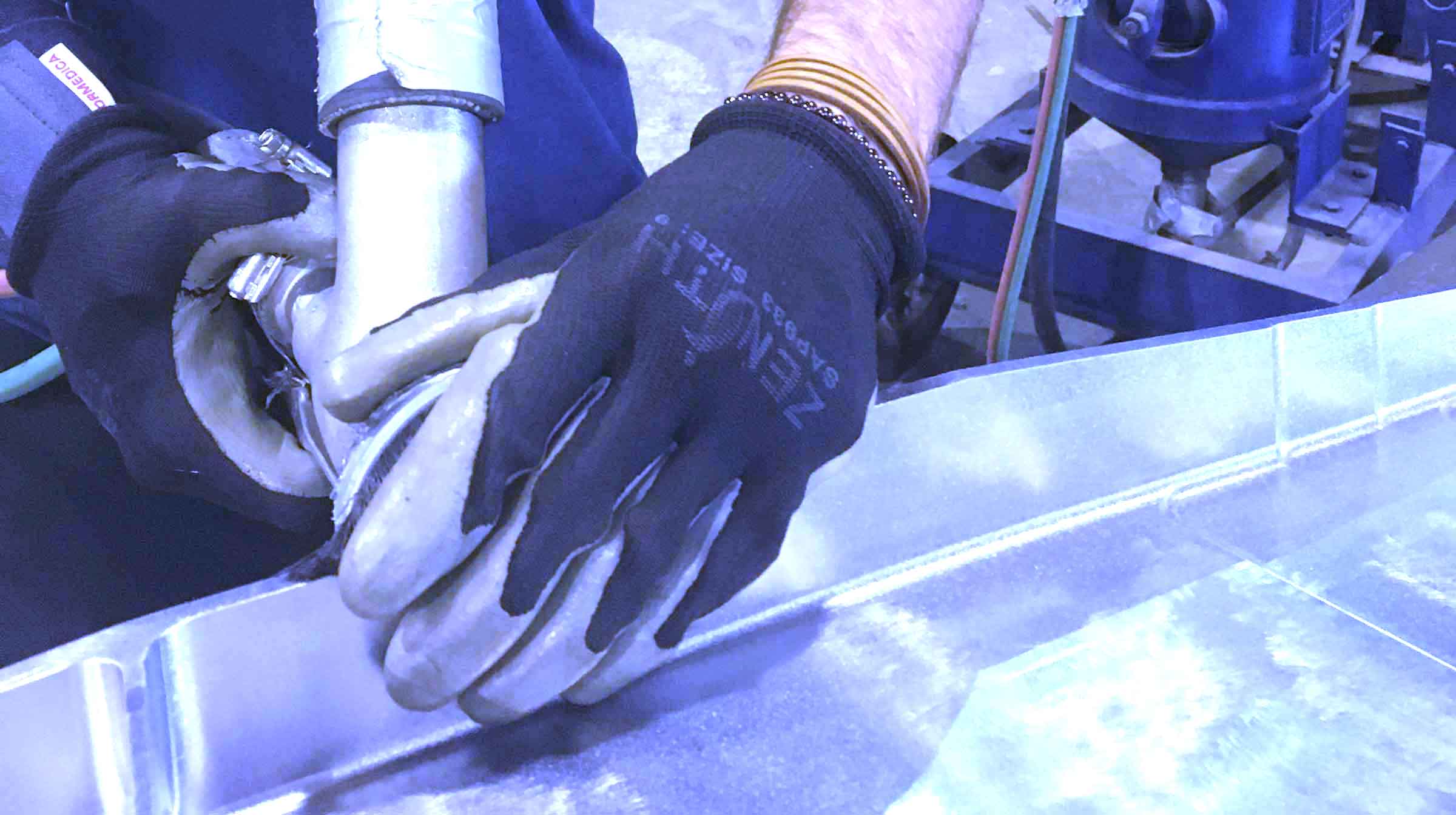
Thanks to portable self reclaim equipment, we have the possibility to provide onsite services if necessary for certain types of repairs or projects. This is especially beneficial in instances when components are too large or cannot be moved.
In addition to the above services, we offer various support services including manufacturabity validation when designing different components. (wing, large component, checking fixtures, etc.) Furthermore, we manage a complete supplier chain for a turnkey approach for a complete product on a single purchase order. (One Stop Shop)